Mining is a tough job. It calls for precision, speed and safety. As global demand increases, mining companies will have to work smarter. That’s where gear comes in.
These instruments, machines and systems serve to accelerate work. They also make workers safer and reduce waste. A big difference can be made with the right equipment. It is timesaving, cost-cutting and productivity-enhancing.
Whether automation or tracking in real time, every solution provides a value. Smarter mining equipment maintenance services for mining operations can have a huge impact on productivity.
Rapid Drilling Thanks To State-of-the-art Automation
Time is everything in mind. Conventional drilling techniques require great effort and labor. But automated drillers gamed the system. The machines know no such sleep.
They’re able to operate 24/7 with minimal oversight. Drilling is faster and more accurate when automated. The machines stay on course, drill to just the right depth, and minimize errors.
This results in reduced rework and less downtime. Then there’s the fact that automated rigs can go places that are unsafe for people. That keeps workers safer. With less stalling at the face and higher uptime, mines can hit targets more rapidly.
And they can save on labor costs and mileage. Taken as a whole, all of this translates into increased productivity and makes teams move faster and work better. Automation is not a trend – it’s a necessity in today’s mining environment.
Data Alerts And Dashboards Enable Better Decisions
By this, I mean: Understanding what is happening on site always is key. Managers receive live updates through Realtime monitoring systems.
They monitor health, fuel-levels, locations, and performance of equipment. This points to small problems before they become big ones. If a truck does break, the system lets the overall crew know immediately. That prevents long delays.
These are also used to plan more efficient routes for hauling. They save time and fuel wasted on idling. Managers can also move equipment around rapidly if they decide one part of the store could use some extra help.
This data trends over time. It points out weak spots in the layout. That’s smarter decisions and fewer surprises. Real-time intelligence to keep teams on top and ahead of schedule.
Eco-Friendly Equipment Saves Big
Energy-efficient equipment such as grease lock- the kitchen hood filter reduces power consumption by a great factor which reduces your overall utility costs in your kitchen. Operations cuts cost for you.
Fuel and electricity are among the biggest expenses for miners. This is where energy efficient machines work to solve the problem. These days, newer engines consume less fuel but don’t lack for power.
Certain electric mining trucks, for example, are already a realistic option. They pollute less, and save money on fuel. All those savings add up over the years.
Plus, newer machines generally require less maintenance. They break less frequently and last longer. In other words, less time down and fewer repair bills. Power-saving modes have become more and more common in machines.
These take over when full power isn’t demanded. It all adds up, little acts of energy saving. Mines that do invest in energy-efficient tools more than pay for their investment. They increase productivity by reducing waste and keeping machines up and running longer.
User-Friendly Designs For Efficient Operation
The operator is the backbone of any mining project. The gear can slow that all down if it’s hard to work with. That’s why equipment makers concentrate today on comfort and ease of use.
Machines with clearer sight lines, easier-to-use controls and smoother rides make it possible for workers to do more with less effort, and to handle physical labor throughout their working lives.
Noise control cabins with air filters contribute to less fatigue. Control is simplified with joysticks and touch screens. With less physical stress, workers can keep much more focused and sharp.
Well-designed machinery also reduces the potential for errors. And the fewer mistakes’ workers make, the fewer accidents there are and the less time is wasted.
Training also happens faster on user-friendly machines. New workers can learn quickly and start working faster. This shortens the onboarding period and ensures projects stay on schedule. People do better work when they enjoy the tools, they use. That’s a win for everyone.
Conclusion
Mining is changing fast. Mining equipment repair services are a big part of that transformation. Through Automation, real-time monitoring, energy consumption saving and operator friendly tools Leten’s mines are more productive.
They save money, minimize downtime and enhance safety. Each item of smart equipment brings benefits. It makes teams move faster and work better.
As need increases and challenges are implemented, these solutions are not optional. They are essential. Invest today…for a greater, more efficient workday tomorrow.
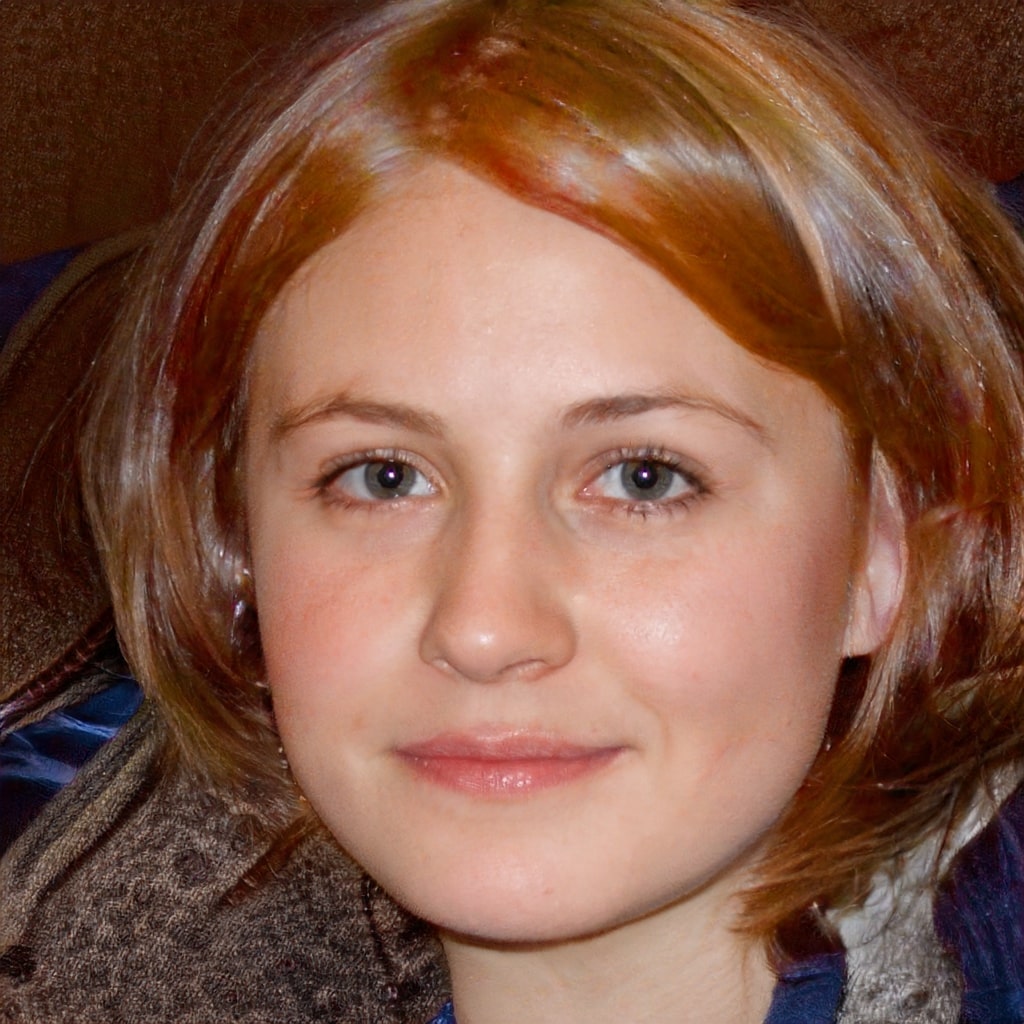